YoungBlood
Well-known member
Okay, here is a few weeks of progress that I haven't had a chance to upload yet.
Homemade driveshaft loop that I made with some scrap bar stock I had and the tubing bender
The finished product
I needed to get an X in this chassis, so I took what was left over of my 2x3 tubing scrap and decided to use it. It might look ugly but it totally works. I put the loop in the middle of the joining 45 degree cuts and braced the insides (and welded the outsides) to make one full piece. Its in there very well. Wish I had more money to do something a little more legit, but this will work
Homemade driveshaft loop that I made with some scrap bar stock I had and the tubing bender
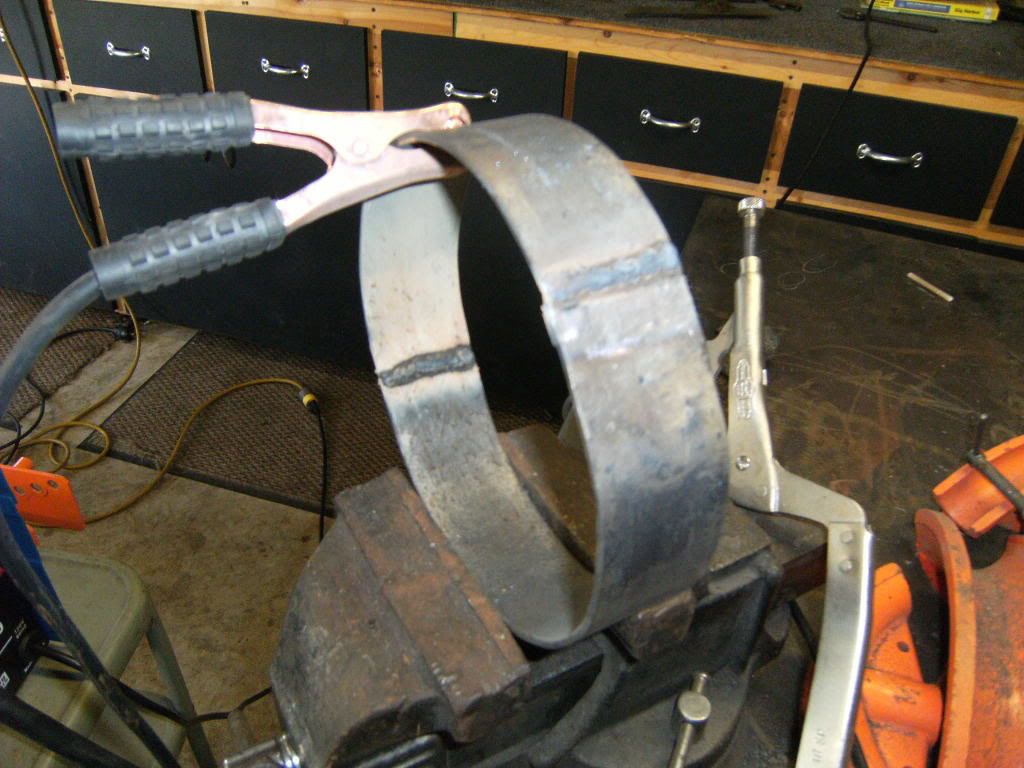
The finished product
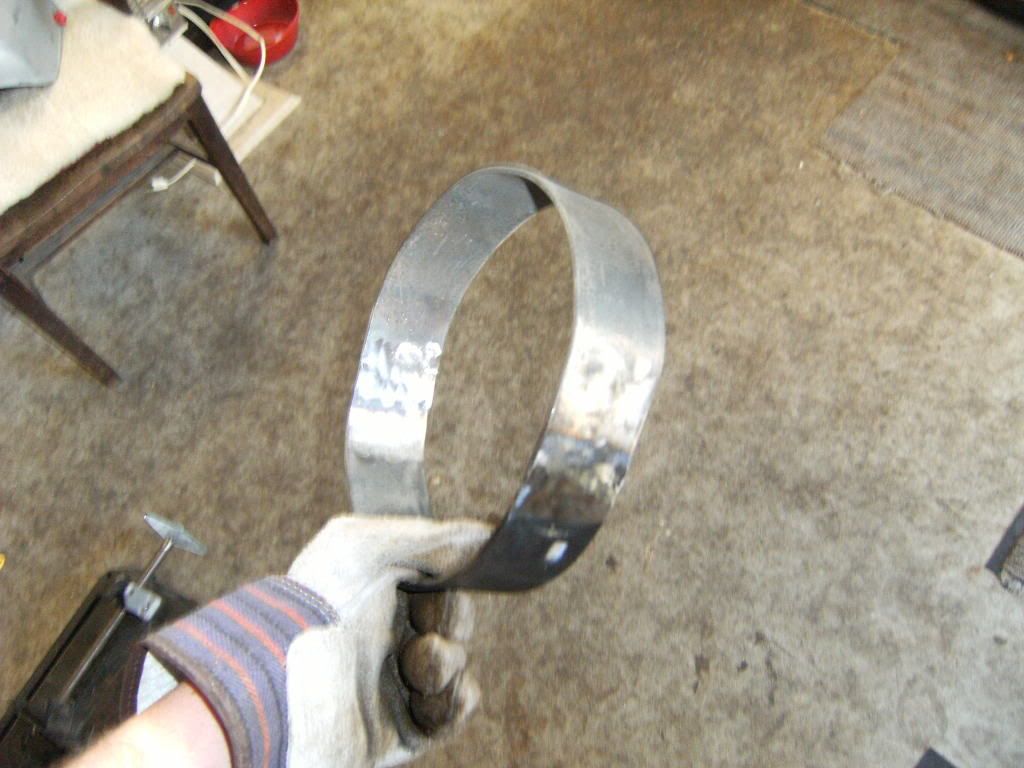
I needed to get an X in this chassis, so I took what was left over of my 2x3 tubing scrap and decided to use it. It might look ugly but it totally works. I put the loop in the middle of the joining 45 degree cuts and braced the insides (and welded the outsides) to make one full piece. Its in there very well. Wish I had more money to do something a little more legit, but this will work
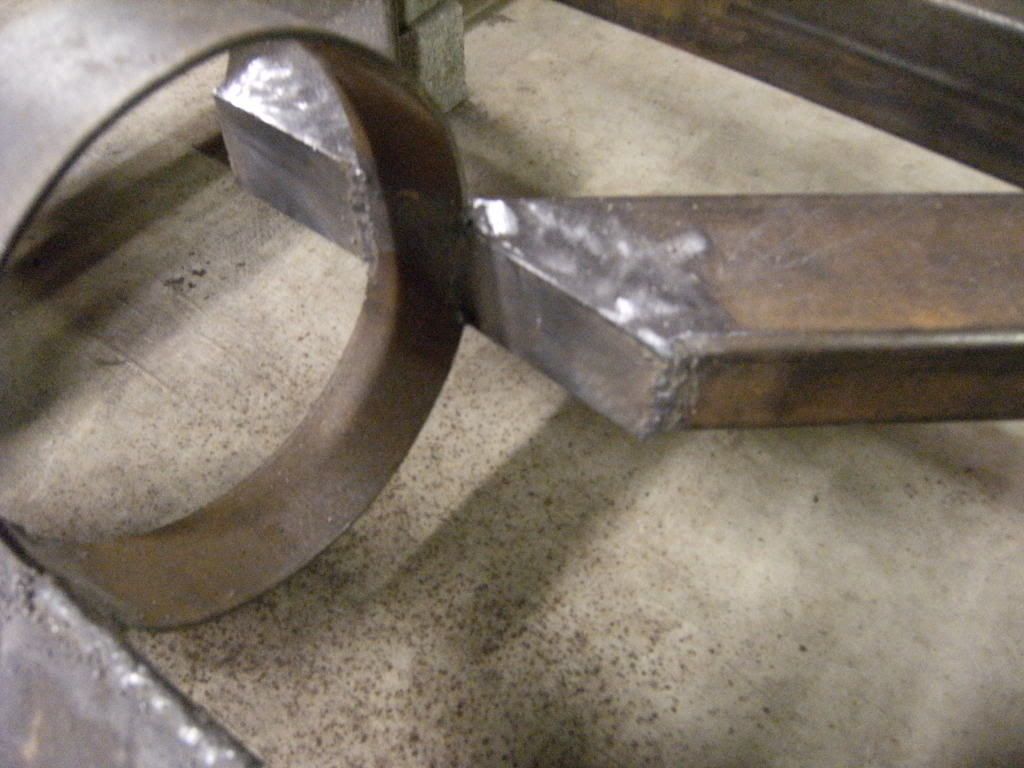
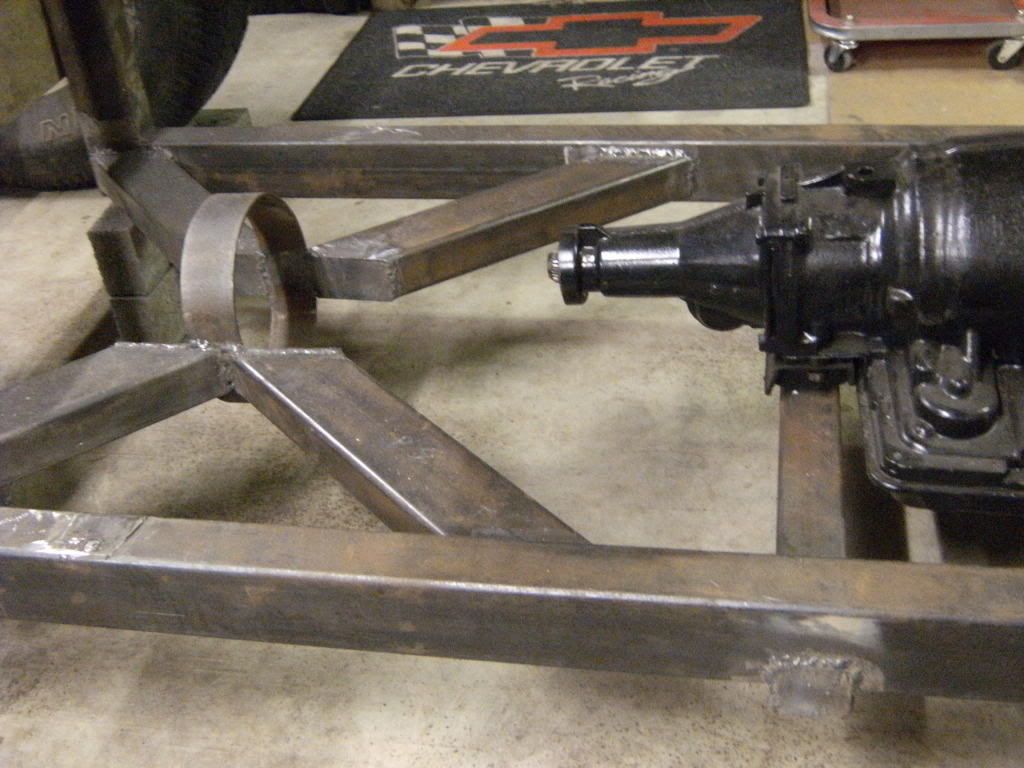